
EN 407:2004 PROTECTIVE GLOVES AGAINST THERMAL RISKS (HEAT AND/OR FIRE)
This standard specifies demands and test methods for protective gloves that shall protect against heat and/or fire. The numbers given besides the pictogram indicates the gloves performance for each test in the standard. The higher number the better performance level.
1. FIRE PROPERTIES OF THE MATERIAL
The ignition time and how long the material glows or burns after ignition is measured in this test.
2. CONTACT HEAT
The glove is exposed to temperatures between + 100°C to + 500°C. Then it is measured how long it takes for the inner side of the glove to become 10°C warmer than it was from the beginning (about 25 ° C degrees). The glove must withstand the increasing temperature of maximum 10°C for at least 15 seconds for an approval.
3. CONVECTIVE HEAT
Here it is measured how long it takes to increase the inside temperature of the glove with 24°C, using a gas lubrication (80kW / m2).
4. RADIANT HEAT
The average time is measured for a heat permeation of 2.5kW / m2.
5. SMALL SPLASHES OF MOLTEN METAL
The test is based on the number of drops of molten metal that generates a temperature increase between the glove material and the skin with 40°C.
A PVC film is attached to the back of the glove material. Molten iron is poured onto the material. The measurement consists of how many grams of molten iron required to damage the PVC film.
According to this standard, characteristics such as abrasion resistance, cut resistance, tearing strength, puncture resistance and impact protection are tested. In conjunction with the pictogram, four numbers and one, or two letters, will be displayed. These signs indicate the performance of the glove.
1. ABRASION RESISTANCE
The material is subjected to abrasion by a sandpaper under a determined pressure. The protection level is indicated on a scale of 1 to 4 depending on the number of turns required until a hole appears in the material. The higher the number is, the better the resistance to abrasion.
2. CUT RESISTANCE, COUP TEST
The cut protection is tested. A knife is passed over the glove material until it cuts through. The protection level is given by a number between 1 and 5, where 5 indicates the highest cut protection. If the material dulls the knife during this test, the cut test ISO 13997(TDM test) shall be performed instead, see point 5.
3. TEARING STRENGTH
Based on the amount of force required to puncture the material with a tip. The protection function is indicated by a number between 1 and 4, where 4 indicates the strongest material.
4. PUNCTURE RESISTANCE
The force required to tear the glove material apart is measured. The protection level is indicated by a number between 1 and 4, where 4 indicates the strongest material.
5. CUT RESISTANCE, TDM TEST ISO 13997
If the knife gets dull during the coup test, see point 2, this test shall be performed instead. The result is given by a letter, A to F, where F indicates the highest level of protection. If any of these letters is given, this method determines the protection level instead of the coup test.
ISO 13997:1999 – Determination of resistance to cutting by sharp objects
An alternative cut test recommended for cut protection gloves. Shall be used in EN388:2016 for cut protection gloves where the cut material dulls the cutting knife during testing. A knife cuts with constant speed but increasing force until breakthrough of the cut protection material. Level of protection is given in Newton, the force needed for cut through at 20mm cut length.
6. IMPACT PROTECTION
If the glove has an impact protection, this information is given by the letter P as the 6th and last sign. If no P sign, no impact protection is claimed.
EN 388:2003
This is the old version of the standard against mechanical risks. The differences compared to the 2016 version are the paper grid in the abrasion test and how to perform testing of cut resistant fibers. Also not applicable to test impact protection.
There are still many protective gloves on the market labeled according to the old version of this standard. These are as good to use as the new marked gloves.
Important to understand is: it’s not the gloves performances that has changed. It is the way of testing the performances that has changed!

EN 388:2016 PROTECTIVE GLOVES AGAINST MECHANICAL RISKS
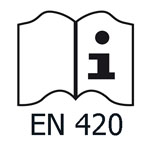
EN 420:2003 PROTECTIVE GLOVES – GENERAL REQUIREMENTS AND TEST METHODS
This standard defines the general requirements valid for all protective gloves:
- The glove itself shall not be a risk to wear or cause injuries to the user.
- The glove material shall have a pH value between 3,5 and 9,5.
- The Chrome VI level in the glove leather must stay at 2,9 mg/kg or below.
- If the glove contains any substances known to cause allergic reactions, it shall be stated in the product information.
- The glove sizes are standardized according to minimum length.
EN 420:2003 has no pictogram.
This standard describes how gloves should be designed to provide hand and wrist protection in welding and similar work situations. Welding gloves shall be tested according to EN 388:2016. They must also provide protection against splashes of molten metal, short-term exposure to open flames, radiant heat, contact heat and mechanical protection according to EN 407:2004.
The gloves are also assessed according to its design and purpose:
- Type A refers to gloves with higher protection against heat but with lower flexibility and dexterity
- Type B refers to gloves with lower protection against heat but with greater flexibility and dexterity
EN 12477:2001 has no pictogram.
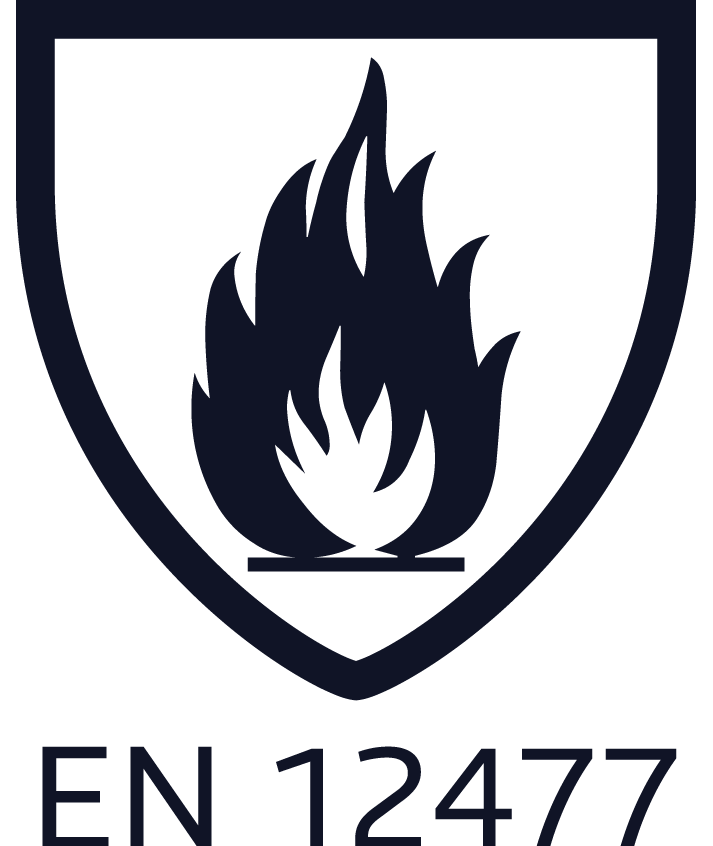